Headquater is in
the centre of Europe
Warranty is up
to 12 months
to 12 months
Best
prices
prices
Savings varies
from 15 to 55%
from 15 to 55%
Shipping
worldwide
worldwide
All shipments
are insured
are insured
Free
shipping
shipping

FAMAGA always strives to provide the best prices and timings of supplies for its customers. We sell only original equipment and spare parts, although we are not always the official distributor or manufacturer's dealer. All displayed trademarks and part numbers are the property of their respective owners.
Our Our product profile contains a wide range of equipment of the Alfa Laval. Alfa Laval manufactures powerful and creative goods that always find the solution for the tough industrial problems at any time. The Alfa Laval achieves the high standards of equipment performance while creating the modern technologies that strengthen the working cycle of the industries. The Alfa Laval Alfa Laval Industrial semi-welded line is one of the flawlessly developed equipment. Alfa Laval Alfa Laval Industrial semi-welded line presents high degree of precision, which offer wide range of automatic and electric resolutions to fulfill all application needs. Because of the high quality of constituents, Alfa Laval Alfa Laval Industrial semi-welded line secure long term functioning.
As a leading industrial supplier of huge number of brands, we always committed to establish splendid experience to our purchasers by offering huge number of industrial outfit and constituent parts at affordable prices with the brilliant chain of supply in the brief period of time. A top level of determination permit us to provide any scale of product in the brief time and satisfy the requirements of our clients in the manufacturing sector. As for the charges and transit period, please fill in the form or submit your order to sales@famaga.us">sales@famaga.us
As a leading industrial supplier of huge number of brands, we always committed to establish splendid experience to our purchasers by offering huge number of industrial outfit and constituent parts at affordable prices with the brilliant chain of supply in the brief period of time. A top level of determination permit us to provide any scale of product in the brief time and satisfy the requirements of our clients in the manufacturing sector. As for the charges and transit period, please fill in the form or submit your order to sales@famaga.us">sales@famaga.us
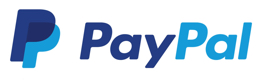
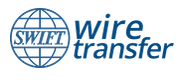
Description
Semi-welded plate heat exchangers are suitable for refrigeration, chemical processes and various kinds of industrial utility duties. The unique Alfa Laval RefTight™ sealing system guarantees a long lifetime sealing between the welded channels because the laser weld is on the outside of the ring gasket groove. The smooth surface ensures a tight uniform seal over the entire gasket ring. Highly efficient and flexible- Space-saving compact unit
- Low operating cost possible owing to superior energy efficiency and prolonged service intervals
- Safe and reliable sealing with no risk of cross-contamination
- Pressure and temperature fatigue resistant
We can compile your order
according to your purchasing list.
This service offers more comfort for our customers. Just upload the list of equipment you need.
Sending...
The message hasn't been sent
The message hasn't been sent
The request has been sent
The request has been sent
To the top of the page
New order
Just now
Manufacturer
Alfa Laval