Headquater is in
the centre of Europe
Warranty is up
to 12 months
to 12 months
Best
prices
prices
Savings varies
from 15 to 55%
from 15 to 55%
Shipping
worldwide
worldwide
All shipments
are insured
are insured
Free
shipping
shipping

FAMAGA always strives to provide the best prices and timings of supplies for its customers. We sell only original equipment and spare parts, although we are not always the official distributor or manufacturer's dealer. All displayed trademarks and part numbers are the property of their respective owners.
Our Our product profile contains a wide range of equipment of the Alfa Laval. Alfa Laval manufactures powerful and creative goods that always find the solution for the tough industrial problems at any time. The Alfa Laval achieves the high standards of equipment performance while creating the modern technologies that strengthen the working cycle of the industries. The Alfa Laval Alfa Laval Compabloc Free Flow is one of the flawlessly developed equipment. Alfa Laval Alfa Laval Compabloc Free Flow presents high degree of precision, which offer wide range of automatic and electric resolutions to fulfill all application needs. Because of the high quality of constituents, Alfa Laval Alfa Laval Compabloc Free Flow secure long term functioning.
As a leading industrial supplier of huge number of brands, we always committed to establish splendid experience to our purchasers by offering huge number of industrial outfit and constituent parts at affordable prices with the brilliant chain of supply in the brief period of time. A top level of determination permit us to provide any scale of product in the brief time and satisfy the requirements of our clients in the manufacturing sector. As for the charges and transit period, please fill in the form or submit your order to sales@famaga.us">sales@famaga.us
As a leading industrial supplier of huge number of brands, we always committed to establish splendid experience to our purchasers by offering huge number of industrial outfit and constituent parts at affordable prices with the brilliant chain of supply in the brief period of time. A top level of determination permit us to provide any scale of product in the brief time and satisfy the requirements of our clients in the manufacturing sector. As for the charges and transit period, please fill in the form or submit your order to sales@famaga.us">sales@famaga.us
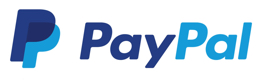
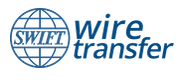
Description
Alfa Laval Compabloc Free Flow is a compact condenser with very high heat transfer efficiency specifically designed for the pharmaceutical industry and the high hygienic requirements of modern API production. The hygienic design, high performance, low operating costs and easy installation combine to ensure patient safety, reliable uptime and production efficiency. Pack more condensing capacity into existing space in your API production- Easy to validate – fully meets the requirements for installation in cGMP processes
- All-welded design and available in corrosion-resistant materials, making it the perfect replacement for graphite block or shell-and-tube
- State-of-the-art hygienic design makes cleaning quick, easy and reliable while low hold-up volumes reduce cleaning solvent usage
- Compact size and low weight enable you to increase capacity even when space is limited – perfect for retrofitting
- Proven low operating and maintenance costs
We can compile your order
according to your purchasing list.
This service offers more comfort for our customers. Just upload the list of equipment you need.
Sending...
The message hasn't been sent
The message hasn't been sent
The request has been sent
The request has been sent
To the top of the page
New order
Just now
Manufacturer
Alfa Laval